When starting a homebuilding or renovation project, one of the most critical elements to consider is the quality of the materials and supplies used. Unfortunately, substandard materials can find their way into the market, putting your project at risk. Whether it’s counterfeit materials, poor-quality products, or suppliers cutting corners to save costs, using these subpar materials can jeopardize the integrity, safety, and longevity of your home. Understanding how to identify such materials and protect yourself from fraud is crucial to ensuring the success of your project. Chris Rapczynski explores below the risks of using counterfeit building materials, offering practical tips on how to safeguard your homebuilding project against such issues.
Understanding the Risk of Fraudulent Building Materials
The building materials industry is vast, and unfortunately, it can be difficult for homeowners to spot low-quality or counterfeit products without the right knowledge. Some common types of fraudulent materials include:
Counterfeit or misbranded materials: These are products that are falsely labeled to suggest they meet industry standards or have been certified when they have not.
Substandard or cheaper alternatives: Some suppliers may offer cheaper materials that look similar to high-quality products but lack the same durability, safety features, or efficiency.
Defective products: These materials may be damaged or produced with manufacturing flaws that compromise their performance and longevity.
Using subpar materials can lead to significant issues, including structural failures, increased maintenance costs, reduced property value, and, in the worst cases, safety hazards.
How to Identify Substandard or Counterfeit Building Materials
Knowing how to identify substandard or fraudulent materials is the first step in avoiding them. Here are several key signs to watch for:
Lack of Certification or Documentation
Reputable manufacturers and suppliers should provide certification or documentation for their products, proving that they meet local or national building codes and standards. If a product lacks these certifications or the supplier cannot provide proof of compliance, that’s a major red flag. Always ask for documentation, including warranty information, test results, and compliance with relevant building codes.
Unusual or Too-Good-to-Be-True
One of the most significant indicators of fraudulent materials is pricing that seems too good to be true. While everyone loves a good deal, a drastically lower price could indicate the material is either substandard or counterfeit. Compare prices across multiple suppliers and be wary of significantly cheaper options. Quality materials typically come at a reasonable cost, and any supplier offering drastically reduced prices might be cutting corners in other areas as well.
Poor Packaging and Labeling
A lack of proper labeling or poorly executed packaging can often point to counterfeit or substandard materials. Genuine manufacturers invest in high-quality packaging that clearly labels the product’s brand, specifications, and certifications. If the material arrives with vague or missing labels, generic packaging, or inconsistent markings, it’s worth investigating further.
Non-Standard Appearance or Quality
Building materials should have a consistent appearance and quality. If something looks “off” or different from the usual product you’ve used in the past, it’s important to investigate. For example, wood that appears too smooth or metal that lacks proper corrosion resistance could be indicative of lower-quality or fraudulent materials. Always check materials for visible defects, inconsistencies, or differences in texture and color.
Limited or Untraceable Supplier Information
Another warning sign is a supplier that provides minimal or vague information about their business or products. Legitimate suppliers are usually open about their business history, product sourcing, and quality control processes. If you can’t find verifiable details about a company or if they seem unwilling to answer questions, this is a potential sign of trouble.
Tips for Ensuring You’re Getting What You’re Paying For
Now that you know how to identify potential red flags, let’s explore some practical steps you can take to ensure the materials you’re using are genuine, high-quality, and safe.
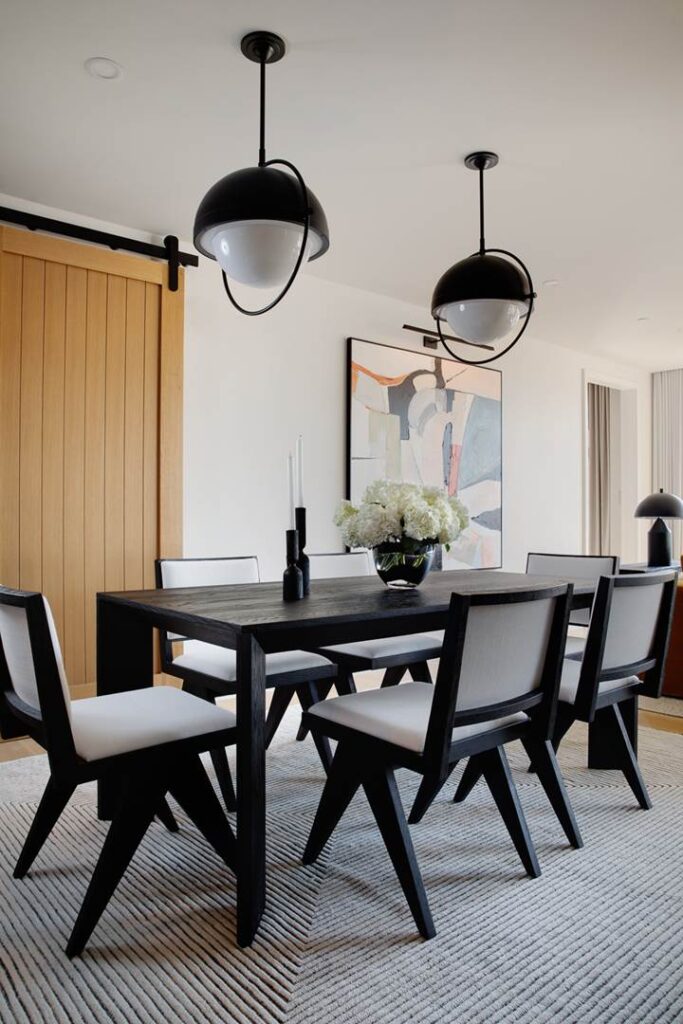
Work with Reputable Suppliers and Contractors
One of the best ways to safeguard your project is to work with reputable contractors who have a proven track record. Take the time to research professionals for your project and check for online reviews or recommendations from others in the industry. Make sure your contractors also have a history of using high-quality materials and can provide evidence of the products they are recommending.
Request Material Samples
Before placing large orders for materials, request samples to inspect the quality. This is especially important for high-ticket items like countertops, flooring, and insulation. Reviewing samples allows you to verify the product’s quality and ensures it meets your expectations before making a full commitment.
Verify Certifications and Testing
Make it a point to verify any certifications associated with the materials you’re purchasing. Most building materials should comply with industry standards such as ASTM (American Society for Testing and Materials) or ISO (International Organization for Standardization). These certifications guarantee that the materials have undergone testing to meet specific performance and safety criteria. Always ask for proof of certification and cross-check it with the relevant authorities.
Consult with an Expert
If you’re uncertain about the materials you’re purchasing, consider consulting with a building expert or engineer. These professionals can help you understand which materials are appropriate for your project and how to spot substandard products. In some cases, an experienced contractor can spot counterfeit or poor-quality materials based on their knowledge and experience in the industry.
Conduct Inspections During Delivery
When your materials arrive, inspect them carefully for any signs of damage, defects, or discrepancies with the order. Ensure that the items match the specifications and are in good condition. If you spot anything unusual, address the issue with the supplier immediately before work begins.
Keep Documentation and Receipts
Always keep receipts and documentation for all the materials you purchase. This paperwork will not only be useful for warranty purposes but also act as a record in case you need to return or exchange defective materials. If a supplier claims the materials are of a certain quality but cannot back it up with documentation, it’s time to find another supplier.
Conclusion
Fraudulent or substandard building materials can have serious consequences for your homebuilding project, from costly repairs to safety hazards. By staying vigilant and educating yourself on how to spot potential fraud, you can significantly reduce the risk of encountering these issues. Working with reputable suppliers, verifying certifications, inspecting materials carefully, and maintaining strong communication with contractors will ensure you’re getting the quality materials your home deserves.
By taking the proper precautions and safeguarding your homebuilding project from fraudulent materials, you’re not just investing in the aesthetic appeal of your home; you’re investing in its long-term safety, durability, and value. Stay informed, ask questions, and never settle for less than the best when it comes to your home.